Specific steps of hot and cold mixing process of PVC injection pellet molding
Published:2022-10-06 Views:1006
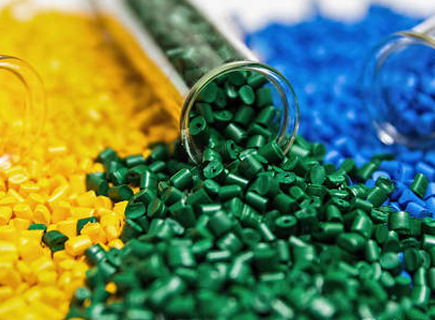
In the mixing process, the material in the machine at high speed friction heat, so the temperature control of PVC injection molding particles is very important, the general temperature control needs to do: PVC resin and additives into the mixer, to immediately stir, using its friction to warm up, when the temperature reaches about 120 ℃ can be discharged into the cold mixer.
Hot material is mixed in the cold mixer, when the temperature is lower than 45 ℃ before the cold mixer gate can be opened to release material. Need to ensure that the cooling water temperature is below 15 ℃. PVC injection molding particles in the mixing process through the density change, homogenization and partial gelation process, all need a certain amount of time to complete. Material melting time becomes longer, the temperature will rise too high, easy to cause the decomposition of the material discoloration, product quality deterioration.
If the mixing time is too short, it will make the extrusion process difficult, so the control of time should be very accurate, which is the key factor affecting the quality of the mixture molding. The selected order of addition should be conducive to the role of additives, to avoid the adverse synergistic effect of additives, but also to improve the speed of dispersion.
For example, ACR is easy to adsorb stabilizer and liquid additives, which will affect its stabilization effect and plasticization effect, so it should be added after stabilizer. If the external lubricant is added too early, it will cover the outer layer of PVC particles and hinder the recombination of PVC particles, which will reduce the degree of denseness, homogenization and gelation speed, so the external lubricant is usually added at the later stage of mixing.
These factors play a key role in the processing of the mixture, so the manufacturer should complete each step strictly at regular intervals to ensure the production of finished PVC pellets of qualified quality.
Application Recommendation